Horizotal Rocket Engine Test Stand
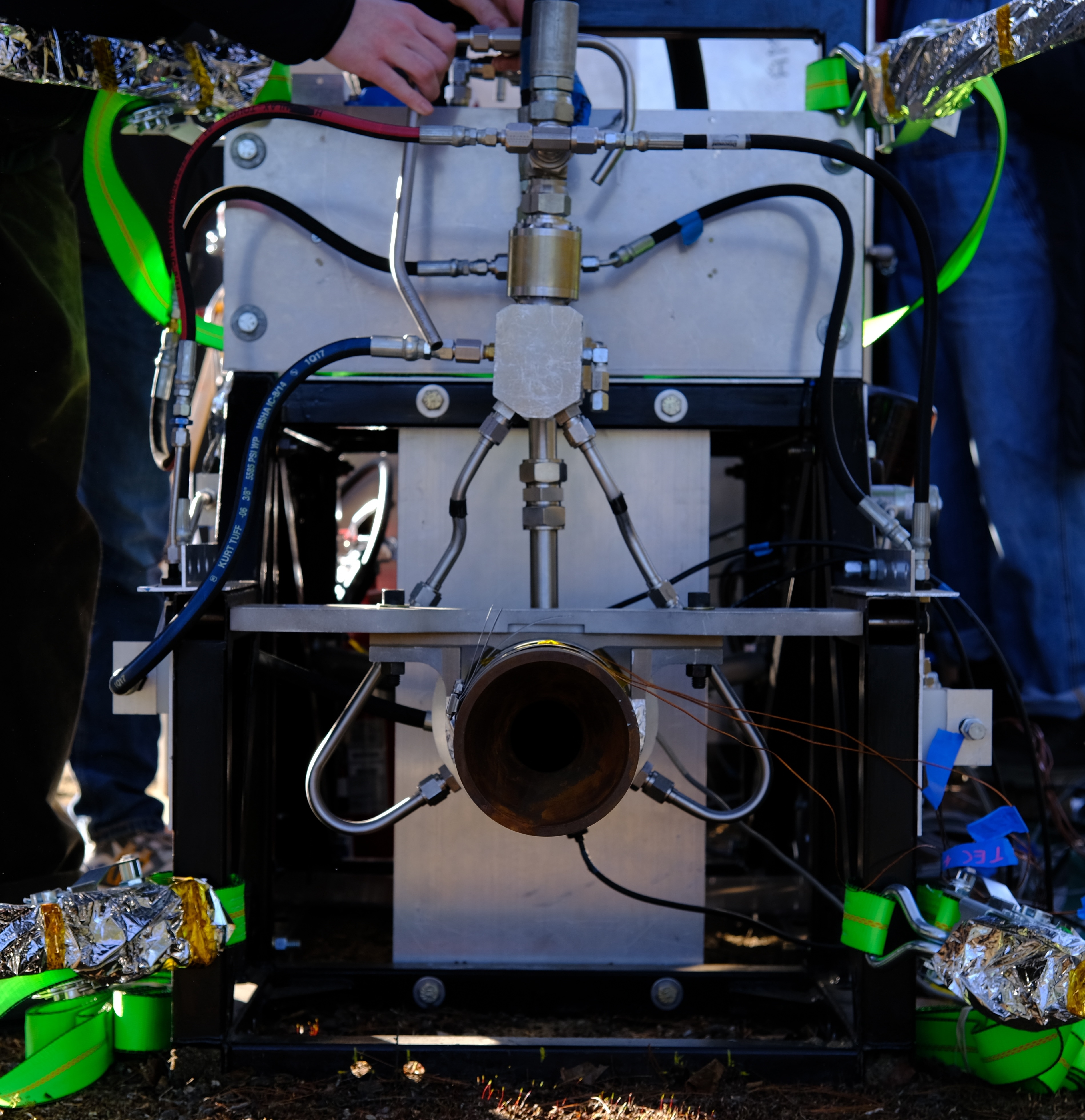
The Horizontal Test Stand with the Iron Lotus engine integrated
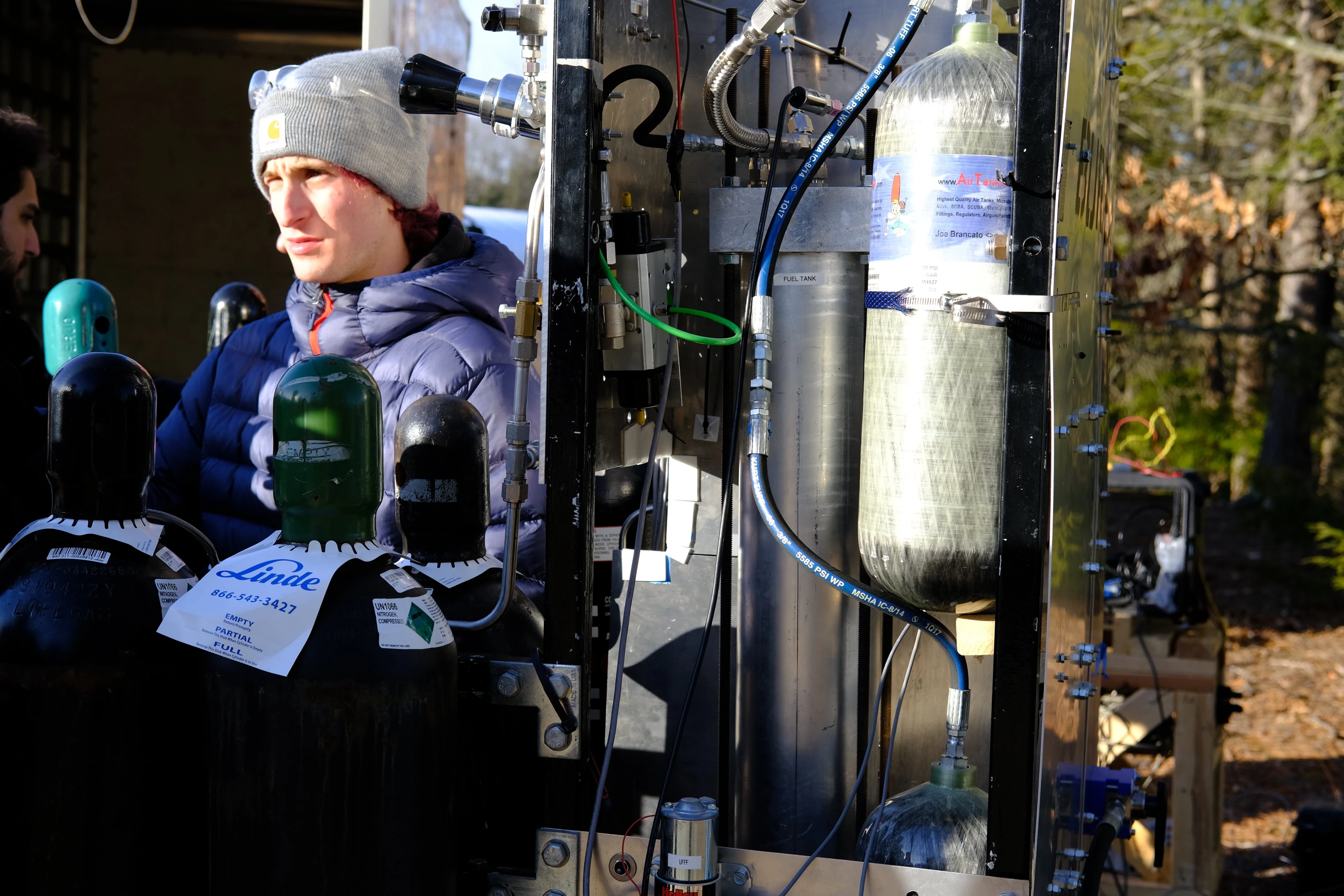
Me standing text to the Horizontal Test Stand just before a successful hotfire test.
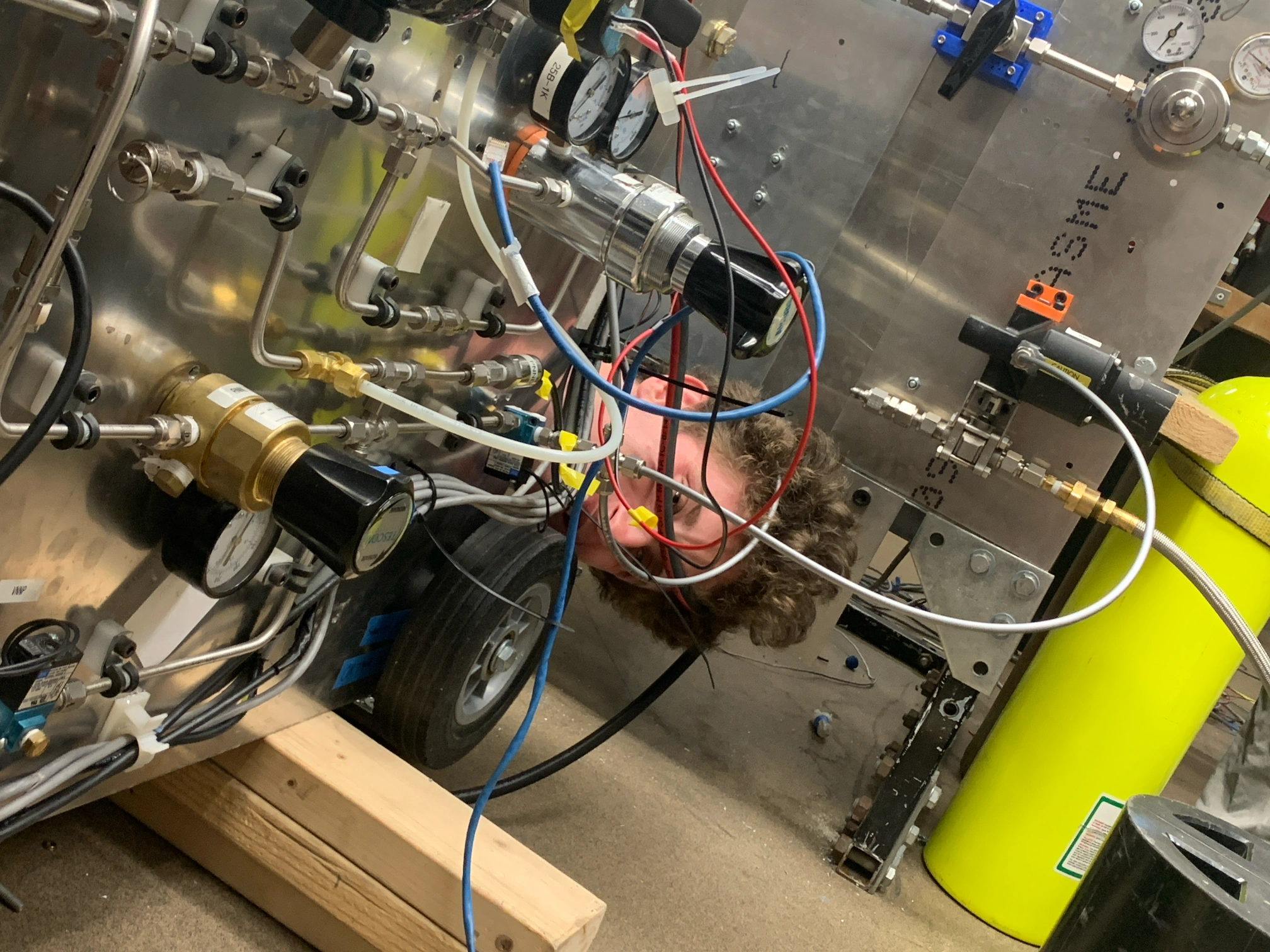
Myself working on the Horizontal Test Stand, peaking out from behind the pneumatics panel as I built the purge system.
Project Overview
The Horizontal Test Stand, or HTS, is the Boston University Rocket Propulsion Group's (BURPG) flagship test stand. Capable of testing engines with up to 10,000 pounds of thrust, the project had been under development for quite a while when I first joined BURPG. The stand had many ambitious goals, including a bang-bang pressurization system. The team's leadership refocused the stand to become the minimum viable test stand to fire the Iron Lotus engine, so work begun to build up a feed system compatible with the engine.
My Contributions
When I first joined BURPG, my first task was to create a 12 volt power supply system for servo actuated ball valves on HTS. I designed, routed, and soldered all wiring for it as well as choosing and mounting a 12 volt power supply to the tank stand panel on HTS. Once I completed all wiring, the test stand was tested in the lab and seemed to work as expected. However, upon deployment, issues were observed with the servo ball valves. Upon returning, all ball valves were removed, and it became the team's job to source solenoid valves and pneumatic ball valves to replace the servos. All valves were replaced and tested, and the stand was ready for another deployment.
For future deployments of the stand, the team wanted a network camera to view the stand while it was unsafe for personnel to be nearby. The network camera purchased did not initially work due to a network configuration issue, and I was tasked with fixing it. I fixed the network camera, as well as rebuilding the stands's electrical ground service equipment (GSE) box, which contains a network switch, power supply, and 12 volt inverter for the test stand's computers, as well as power over ethernet (PoE) injectors for the antenas used to communicate with the test stand from far away. The full setup was tested in the lab, and worked once deployed to the test site.
As the team deployed the stand, a group of members referred to as the red team had the task to ensure the test stand was prepared for propellant load and test. I was placed on the red team, with my tasks being to run dry and wet clicks of the test stand and troubleshoot any issues that appear with the stand, as well as connecting and opening both gaseous nitrogen and nitrous oxide gas bottles to the test stand. Additionally, I installed the igniter in the Iron Lotus engine. After the test stand fired, I would be one of the first people to return to the test stand and ensure the system is safed and clear to approach for the rest of the team.
Once elected to the executive board, I became the test director for all HTS tests. This meant I was responsible for ensuring the safety of all team members, as well as running all test operations and ensuring that all test objectives were acheived, and all procedures are completed correctly.
I am now leading the team in upgrading the test stand. This includes making more of the flex hoses on the test stand into metal flex tubes, introduce a differential pressure transducer to measure the fill level of the oxidizer tank, and introduce a high flow regulator to the fuel tank. Additionally, we are planning to support cryogenic oxidizers, allowing the test stand to work with almost any propellant that the team can get its hands on. The stand will also be prepared for the team's future engines, so that they can be tested as quickly as possible on a working and characterized test stand.
Watch the static fire test
For the first static fire test of the Horizontal Test Stand, I was in charge of coordinating the red team's final tasks so that we could exit the test site quickly and safely once all were complete. I was the one to open the nitrous oxide bottles, as well as insert the igniter. Additionally, after successful static fire, I was among the first people to return to the test stand, and was responsible for closing and safing nitrous oxide systems on the test stand.