Icarus
Project Overview
Icarus is a liquid bipropellant rocket that runs on Nitrous Oxide and Isopropyl Alcohol. It produced a maximum of 2,000 pounds of thrust, and flew in March of 2025 to 12,900 feet, setting a record for the highest thrust of a collegiate liquid rocket to fly. It is designed to be a minimum viable rocket to get the Boston University Rocket Propulsion Group off of the ground. Icarus was designed, built, tested, and flown rapidly, going from the first element of design to tested in just over two years. A team of 25+ member work on Icarus, with tasks ranging from structural design to propulsion (my team) to custom electronics. When brought together, the result is pretty cool.
Icarus launching.
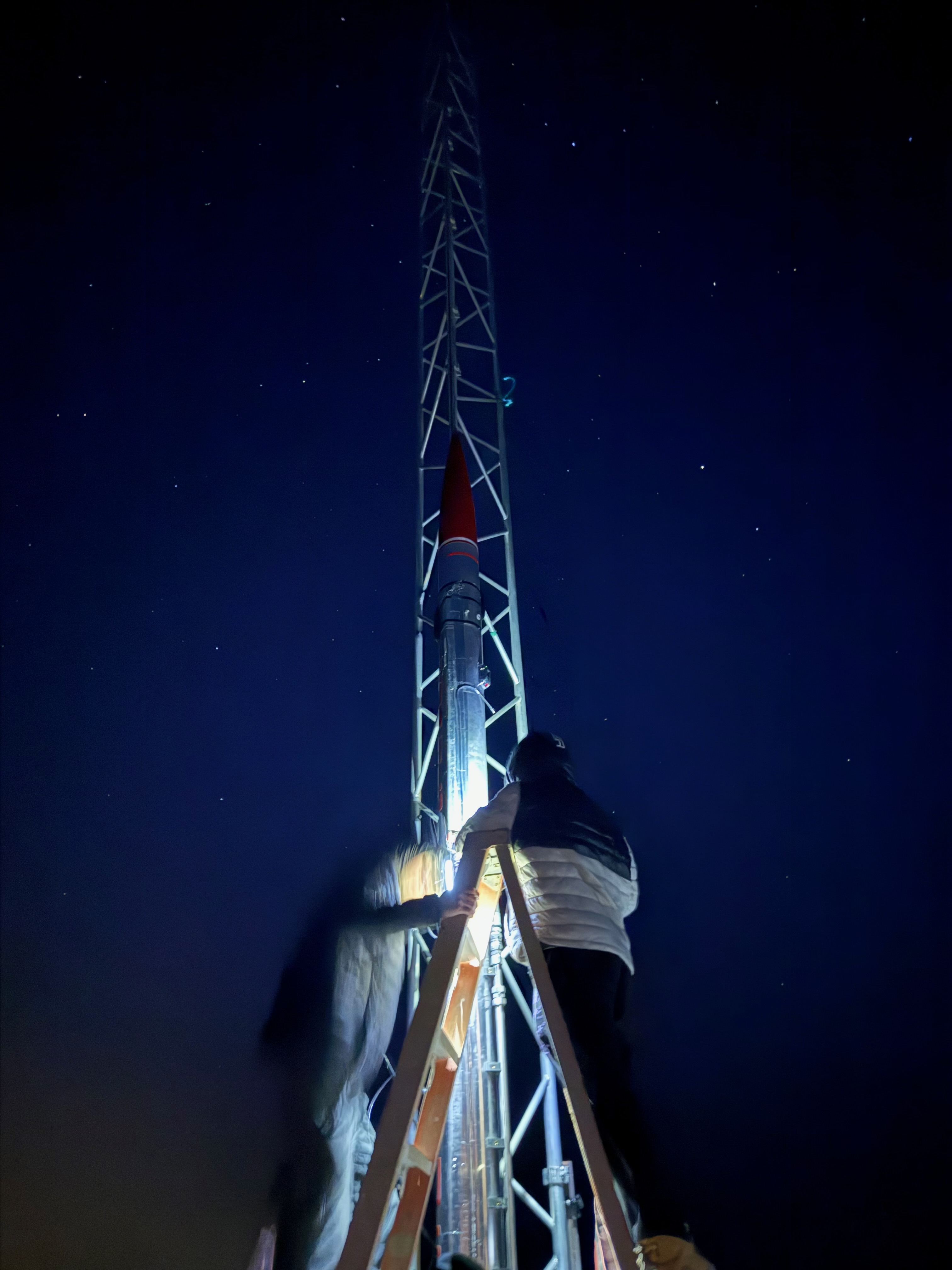
Icarus on the launch rail at night.
Myself and the members of the closeout "red" team posing shortly before a successful long duration hotfire test.
My Role
I serve as the responsible engineer and lead for all fluids and propulsion systems on the rocket. I lead 5+ members of the fluid and propulsion team, where collectively we design, build, test, and operate all fluid and propulsion components of the rocket. Additionally, during testing of the rocket, I serve as the test director, ensuring that all personnel are safe, all procedures are completed correctly, and that all test objectives are met. After tests, I verify all performance and test data and troubleshoot any issues related to performance of the rocket. Since the successful ground test campaign of the rocket wrapped up, I have been responsible for the final flight simulations of the rocket, to determine the likely landing location of the rocket, the maximum altitude, and various other key parameters for members of the team. Additionally, as an executive board member, I am one of 4 people who arrange all operations and logistics to get both the rocket and the team from Boston to the Mojave desert for launch.
Timeline
And what my team has done
Myself and the avionics RE Tim conducting checkouts of the ground service equipment box during a test.
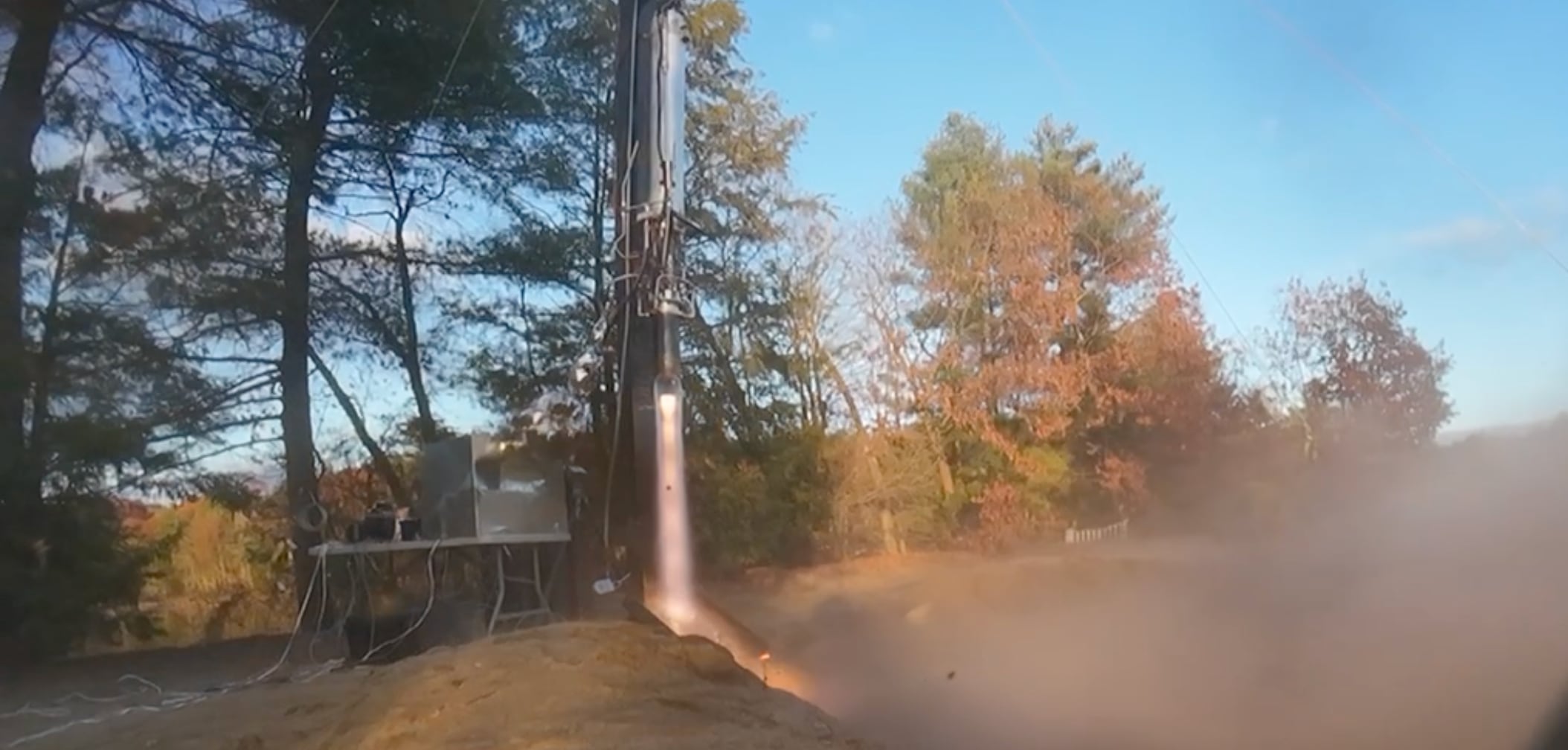
Action cam footage of Icarus during its successful long duration hotfire test.
-
April 2023
The first P&ID for the vehicle is created, and the tanks and domes are designed, undergo a critical design review, and are sent out for manufacturing.
-
May 2023
My team begins design of all fluid components on the vehicle and the ground service equipment, with cost and lead times as the driving factors. We give ourselves a deadline of September to beging assembly.
-
September 2023
Tanks are assembled, and hydrostatic tank proof tests are conducted by myself and the rest of the fluids team. The tanks are verfied and handed over to the structures team for intertank assembly.
-
October 2023
The ground service equipment box components arrive and it is assembled over the course of the month. In the mean time, the tanks are stacked and the thrust structure is assembled.
-
February 2024
The rocket is fully assembled and all fluids and propulsion components are integrated in their ground test campaign configuration, and the rocket is ready for testing.
-
March 2024
The rocket undergoes an extensive test campaign including multiple cold flows, which allow us to characterize the feed system.
-
November 2024
Icarus undergoes a successful long duration hotfire. This concludes the ground test campaign and the rocket is now ready for flight in late March of 2025.
-
March 2025
Icarus flies to 12,900 feet under 2,000 pounds of thrust, setting a record for the highest thrust of any collegiate liquid rocket to fly.
More of my work on Icarus
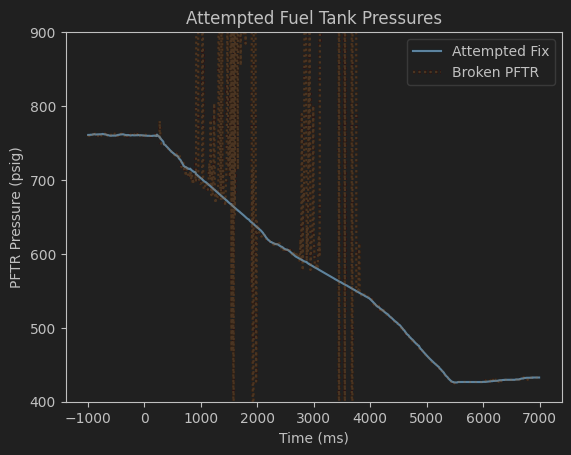
During our long duration hotfire, the fuel tank pressure transducer encountered a soft short to ground, causing an erratic reading. Utilizing the pressure in the fuel plenum, some quick adiabatic tank drainage math, and some simple filtering, I was able to save the data from the test. For all tests, I complete a full data analysis of the test to identify fluid and propulsion system performace.
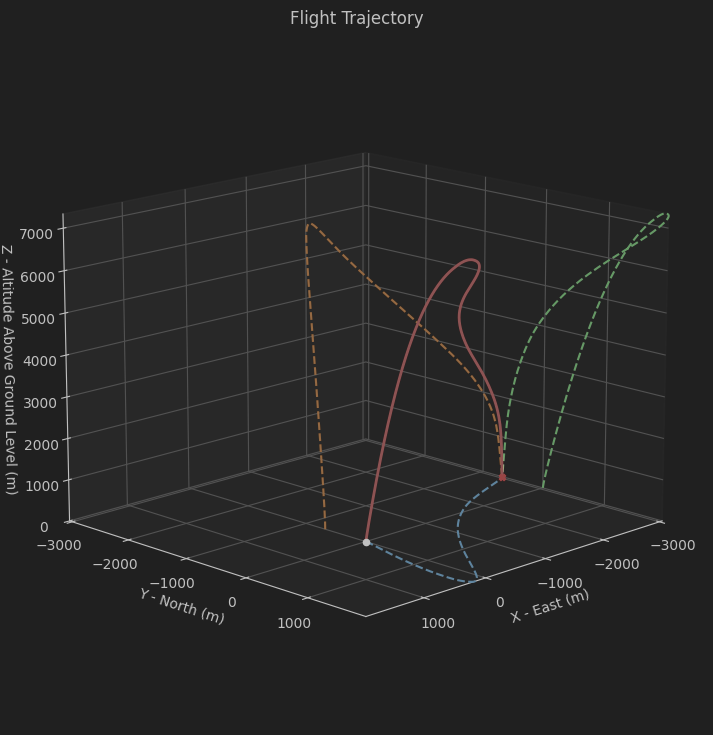
Following our long duration hotfire, I created a 6 degree of freedom simulation of the rocket using python, and found many parameters key to other members of the team. Additionally, I created Monte-Carlo simulations of the rocket to find an estimated landing region of the rocket.
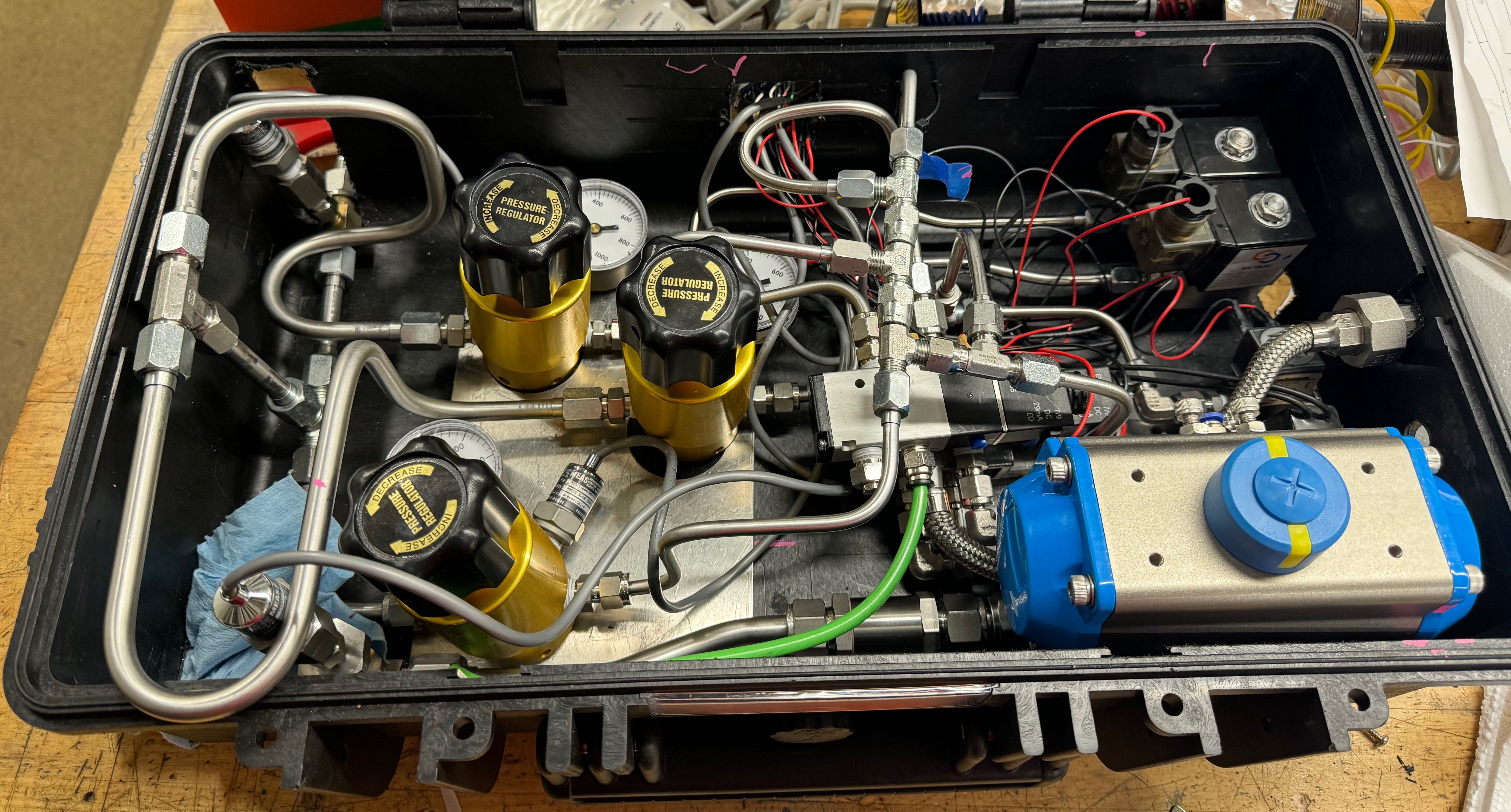
The ground service equipment (GSE) box used to pressurize tanks, actuate main valves, purge the engine, and more. It was designed to fit within a compact pelican case for ease of transport, and allows rapid deploying of the system and the ability to test the system modularly, rapidly accelerating test operations. I defined all requirements for the system, conducted component selection, undertook all design work, and helped assemble and test the box.
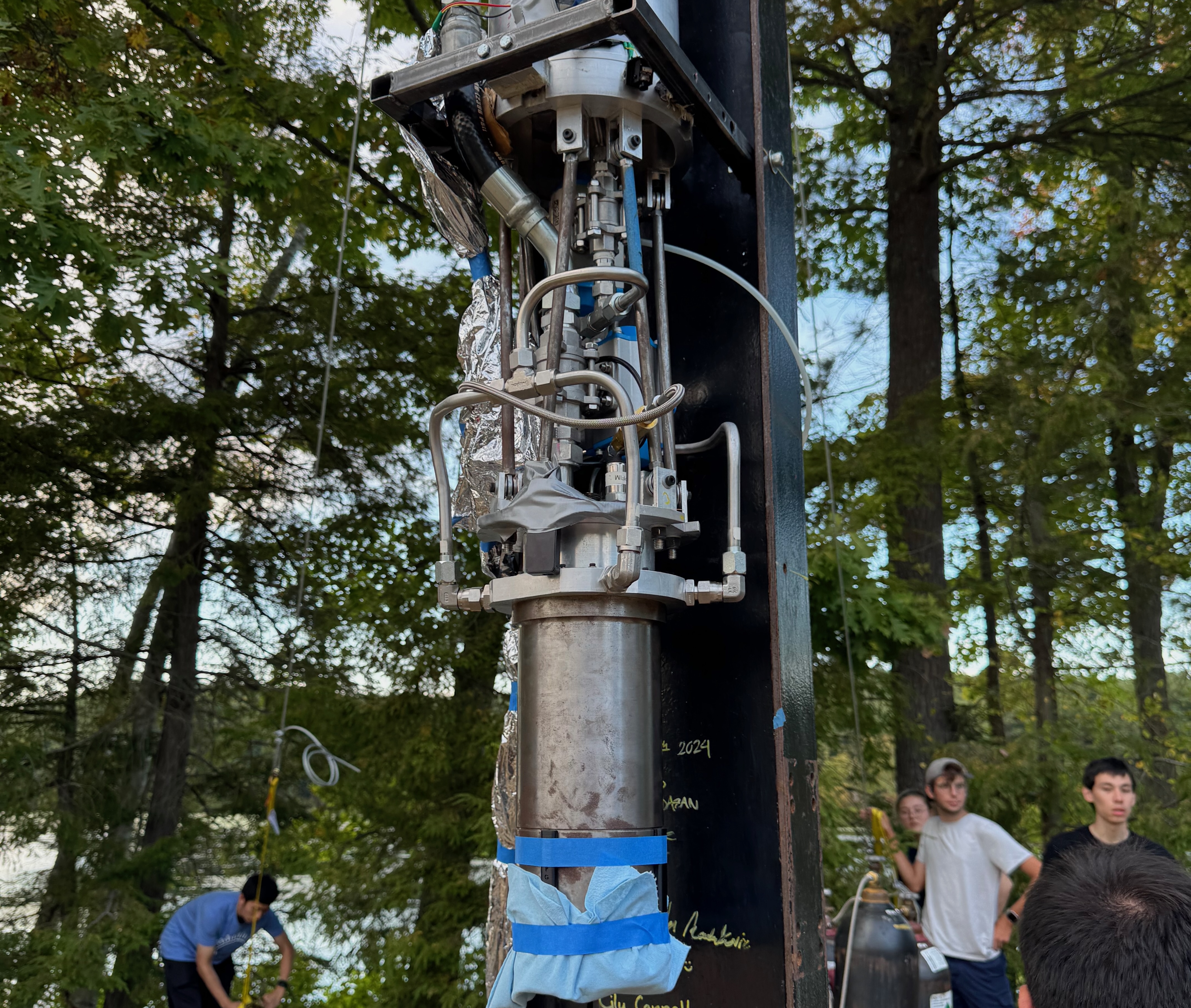
Icarus utilizes 2 simple industrial single acting ball valves, which were chosen for being reliable and as cheap as possible. I modified the ball valves, changing their normal state from closed to open, and additionally replaced the actuator on the oxidizer main valve to a smaller actuator so that it may fit in the thrust structure.
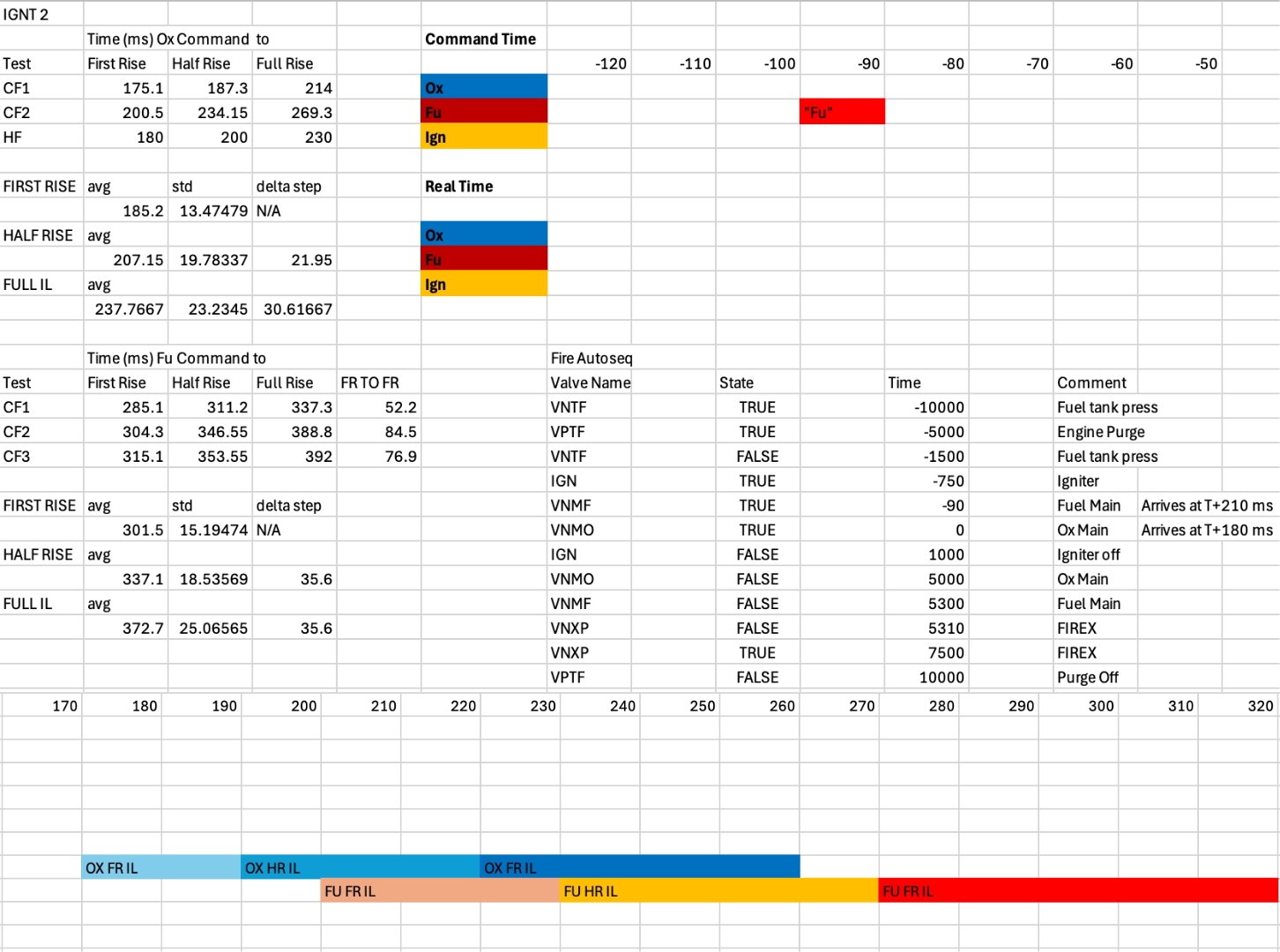
To start Iron Lotus, Icarus' engine, the times of when the igniter goes off and when the fuel and oxidizer arrive are essential to a smooth engine startup. Utilizing data from cold flows, where only one propellant is sent through the fluids system, I was able to determine the ignition timing that successfully lit the engine, as can be seen from the video above.
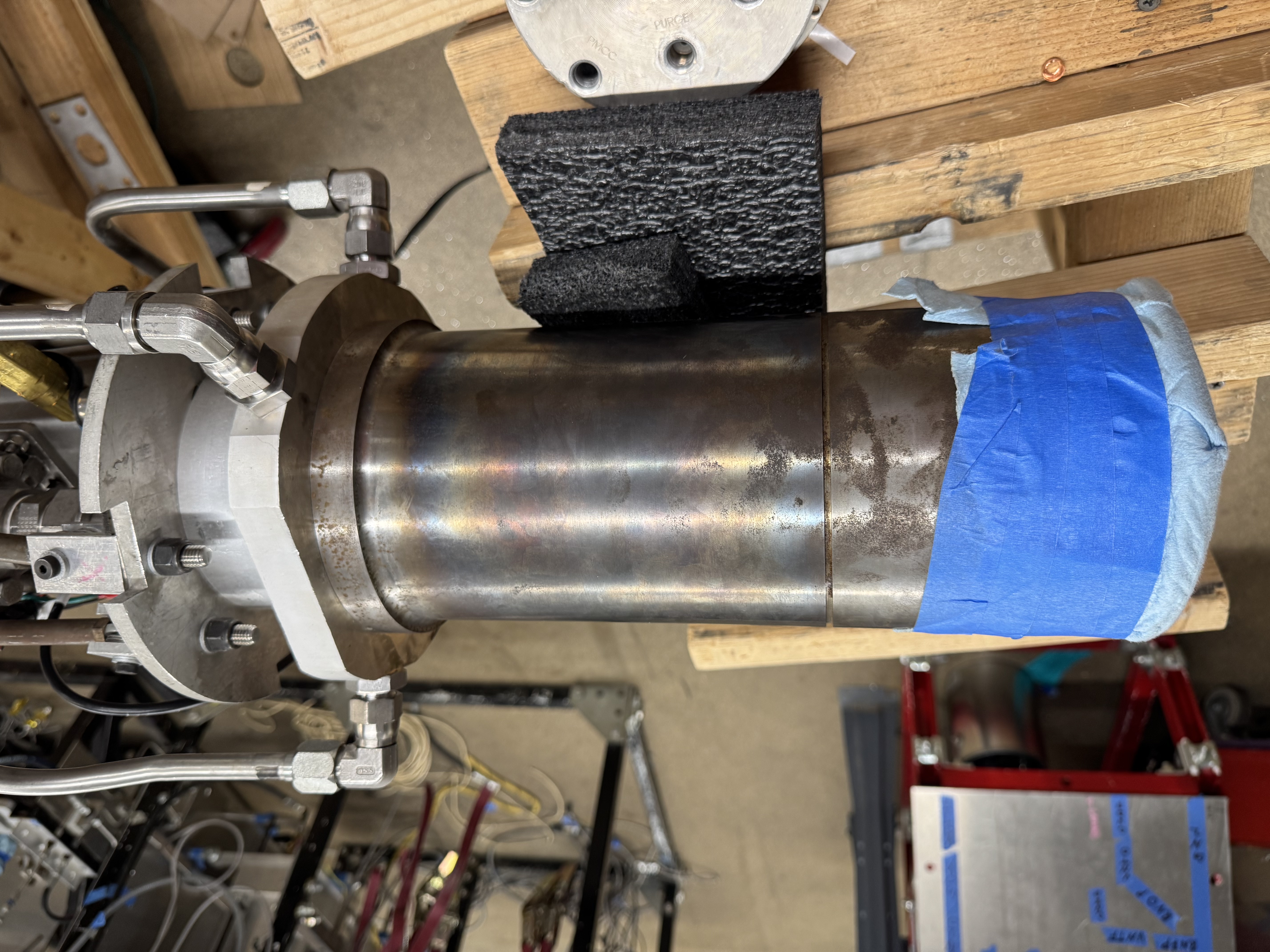
The Iron Lotus engine integrated on the Icarus rocket, with routing bent and routed. I routed all tubing from the tanks to the engine, working around structural elements. I also sized all the tubes to accomidate the appropiate mass flow rate while balancing tube diameter and mass flow rate.
Lessons
Getting a rocket off of the drawing board is not an easy task. I could dream of ideal performance, with so many nice-to-haves, and just imagine it working immediately. In reality, there's always some issue in your build. One of the great lessons I've learned from Icarus is to just get the rocket to testing. Design, build, and test each component as soon as you can. Testing will find some issue, and it may undo all your hours spent optimizing. Finally, don't get stuck on one problem in the field. If you have the bandwidth, always work in parallel and reduce the time to your test. A test day always goes quicker than you think.
Getting to lead a team is one of the greatest privileges I've ever had, and getting to work with an amazing team on a project of this scale is nothing short of incredible. The incredibly talented, hardworking people who I have worked alongside on this project make the entire thing possible, and I am so grateful to be able to call them my team members.
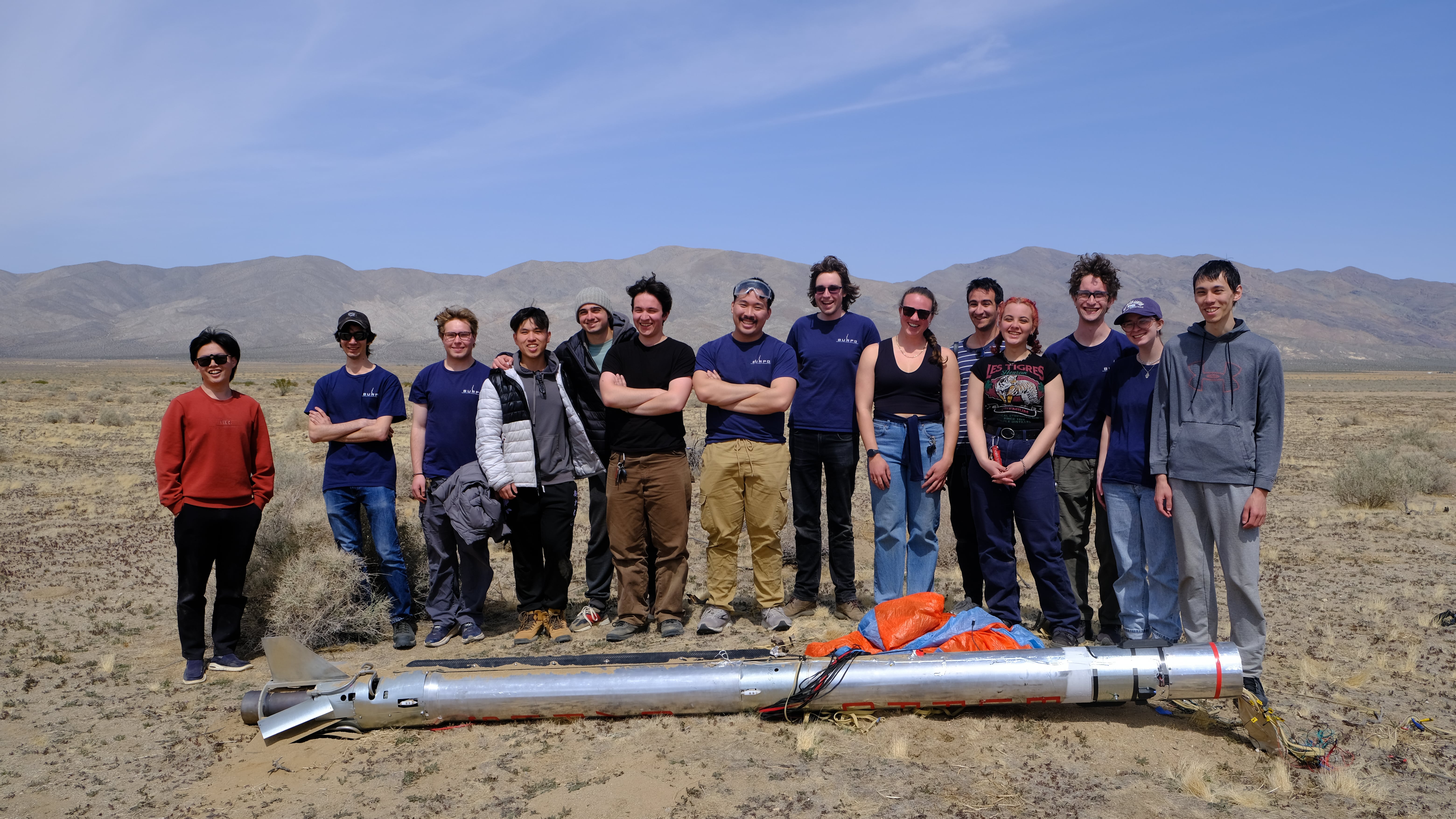
Some of the incredible people who have worked on Icarus. None of this would've been possible without their skill, perseverance, and enthusiasm.